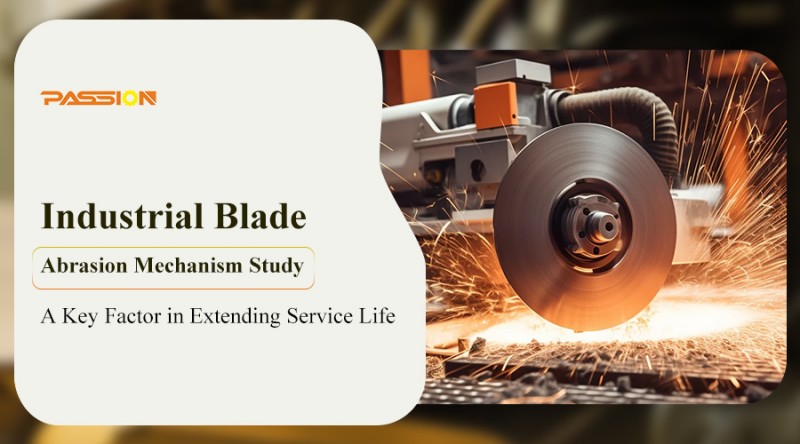
У галузі промислового виробництва стирання лез завжди було важливим фактором, що впливає на продуктивність та якість продукції. З прогресом науки та техніки та постійною оптимізацією процесу, дослідження щодопромислове лезоМеханізм стирання стає все більш поглибленим, спрямований на пошук ключових факторів для продовження терміну служби леза.

Існують різні причини стирання лез, в основному, включаючи механічний знос, тепловий знос, хімічний знос та дифузійний знос. Механічне стирання в основному викликається твердими частинками в матеріалі заготовки для виготовлення канавок на поверхні леза, і таке стирання особливо очевидно при різанні з низькою швидкістю. Теплове стирання обумовлено великою кількістю тепла, що утворюється в процесі різання, що призводить до пластичної деформації стирання леза або теплових тріщин. Хімічний знос - це кисень у повітрі при високих температурах та хімічна реакція матеріалу леза, утворення сполук низької твердості, чіп, що призводить до стирання леза. Дифузійне стирання, з іншого боку, полягає в тому, що під час процесу різання хімічні елементи на контактній поверхні заготовки та стирання леза дифузні один з одним у твердій стані, змінюючи композиційну структуру леза і роблячи його поверхневий шар крихким.
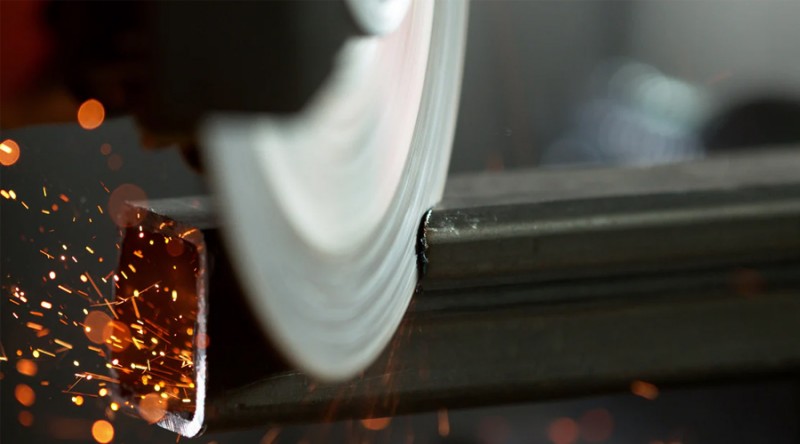
Для цих механізмів зносу дослідники запропонували різноманітні методи продовження терміну служби стирання леза. Перш за все, розумний вибір матеріалів леза є ключовим. Відповідно до характеристик обробленого матеріалу та умов різання, вибір матеріалу леза з достатньою твердістю, стійкість та міцність може ефективно зменшити стирання. Наприклад, під час обробки важких розрізаних матеріалів з великою тенденцією до затвердіння слід вибирати матеріал леза з сильною стійкістю до холодного зварювання та сильної стійкості до дифузії.
По -друге, оптимізація параметрів геометрії леза також є важливим засобом продовження терміну експлуатації служби. Розумний кут леза та форма леза можуть зменшити силу різання та різання тепла та зменшити стирання леза. Наприклад, відповідне зменшення кутів передньої та задньої частини та використання більшого негативного нахилу краю може зменшити знос рісосожної кромки. У той же час шліфування негативної камери або краю дуги також може посилити міцність кінчика леза і запобігти чіпінгу.
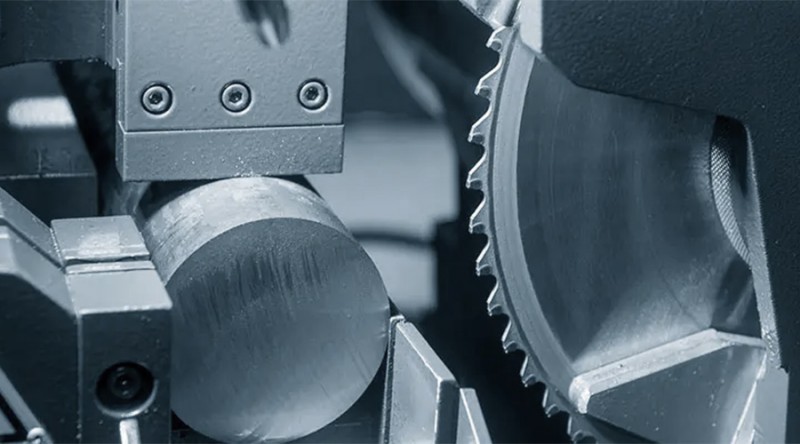
Крім того, розумний вибір дозування різання та використання мастила охолодження також є ефективним способом продовження життя леза. Глибина вирізання та подачі занадто велика, сила різання збільшується, а стирання леза прискорюється. Тому під передумовою забезпечення ефективності обробки кількість різання повинна бути зведена до мінімуму. У той же час використання мастила охолодження може поглинати і забрати більшу частину тепла в зоні різання, покращити умови розсіювання тепла, зменшити температуру різання леза та заготовки, тим самим зменшуючи стирання леза.
Нарешті, правильний метод експлуатації та жорсткість системи процесів також є факторами, які неможливо ігнорувати. У процесі різання лезо повинно спробувати зробити лезо не нести або менше нести раптову зміну навантаження, щоб уникнути леза через нерівну силу та поломку. У той же час, щоб переконатися, що система процесів має хорошу жорсткість, зменшити вібрацію, також може ефективно продовжити термін служби леза.
Підсумовуючи, ключові фактори для продовження терміну експлуатації промислових вставок включають розумний вибір матеріалів леза, оптимізацію параметрів геометрії лопатей, розумний вибір дозування різання, використання мастила охолодження та правильні методи експлуатації та жорсткість системи процесів. Завдяки постійному поглибленню досліджень механізму стирання лез, вважається, що в майбутньому з’являться більш інноваційні технології та методи, вводячи нову життєву силу в розвиток промислового виробничого поля.
Пізніше ми продовжимо оновлювати інформацію, і ви зможете знайти більше інформації на нашому веб -сайті (AcoreStool.com).
Звичайно, ви також можете звернути увагу на наші офіційні соціальні медіа:
Час посади: 15-2024 листопада